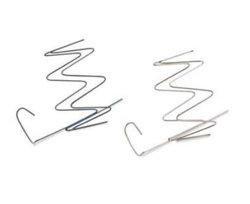
When your clients are manufacturers creating intricate parts for life-saving medical implants, “customer service” comes with more than the usual requirements.
Our customer service is built around ensuring consistently high-quality results for critical metal parts because our customers have no room for error. And with decades of expertise and collaboration with engineers across industries like medical device manufacturing and aerospace, we’ve honed our processes to achieve an unmatched level of precision and consistency.
No two parts are alike and our processes are tested and customized down to the smallest aspect.
R&D Validation Establishes Optimal Level of Stock Removal for Implant Part
When the maker of a cardiovascular implant recently needed to determine the precise amount of stock removal that would produce the best results for a tiny arterial clip made of Nitinol, we made our engineering staff available for a series of tests to evaluate the microfinish improvement at various levels of stock removal.
Our client was managing tight deadlines as part of the FDA approval process. To eliminate the time it would take to send samples back and forth, we arranged to bring the client into our facility in Chicago on short notice to spend a day with our engineers evaluating various levels of material removal in real time.
This allowed the Able team to learn much more about the part application, critical features, and specific measurements required to determine the thickness before and after electropolishing.
The process included a series of precise measurements and analysis using a variety of tools that included a micrometer, profilometer, and microscope. In collaboration with the client, we were able to determine the precise specifications for microfinish improvement and stock removal.
We were also able to provide our client with a deeper look into our processes, engineering, and tooling.
Electropolishing is a highly controllable process that can create a uniform and ultra-smooth surface finish within very tight tolerances. It can remove burrs and other surface imperfections from Nitinol parts with a level of precision and consistency unmatched by other finishing processes. Electropolishing also leaves Nitinol parts with enhanced resistance to corrosion.
Our efforts and collaboration in this case resulted in a safe and effective part – and left our client on track for FDA approval on a challenging timeline.
Consistent, High-Quality Results for Critical Medical Parts
Why do so many medical manufacturers trust Able Electropolishing for the highest quality results for their critical metal parts? Because that’s what our processes deliver, time after time.
Learn more about Able Electropolishing for a wide variety of specialty alloys including Nitinol – and about our Finish First prototyping for ensuring the best possible finishing results from the start.