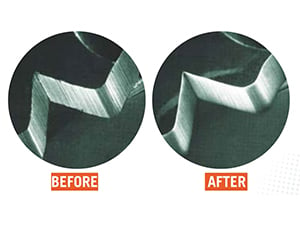
When it comes to precision metal finishing, trust is earned through consistency, quality, and a deep understanding of what’s at stake. For many industries, there is no room for error in their critical metal parts. That’s why, for over 70 years, Able Electropolishing has quietly set the standard — not just in electropolishing, but in what it means to be a truly reliable partner in high-stakes manufacturing.
From life-saving medical devices to mission-critical aerospace components, companies across the most demanding industries rely on Able’s electropolishing and passivation services to ensure their parts meet the highest standards of performance, cleanliness and durability.
Built on Innovation, Grounded in Experience
Founded in 1954 by Zenon Pokvitis, a self-taught chemist and Army veteran, Able Electropolishing emerged from a time of explosive industrial progress. Pokvitis took the breakthroughs of World War II and channeled them into practical surface finishing solutions for the manufacturing world. His legacy of innovation and hands-on problem solving has carried forward through three generations of family leadership.
Today, Able operates a 50,000-square-foot facility in Chicago and employs 150 team members across three shifts. This state-of-the-art operation includes automated finishing lines, customized pre- and post-cleaning stations, and a validated process built to meet the most rigorous demands in the field.
Validated Processes
Able’s electropolishing and passivation processes are validated. This level of process control benefits every customer, not just those in healthcare and aerospace. It ensures that every part is finished consistently within tight tolerances, backed by statistical process control (SPC) data and reinforced through documented inspections.
Able holds certifications that include ISO 9001:2015, ISO 13485:2016, and AS9100:2016 to serve industries where the cost of error is measured in lives, safety, and system failure — not just missed deadlines.
A Process Designed Around You
Every part that enters Able’s facility undergoes a tailored, multi-step treatment. From pre-cleaning to electropolishing, post-cleaning, and final packaging, each stage is designed to ensure the best results for the geometry, material, and end use of the part.
In addition to rigorous quality checks, Able also offers in-house testing and analysis capabilities. Our facility is equipped with advanced tools for surface profiling, microscopic inspection, and elemental analysis, making it possible to verify electropolishing results down to nanometers.
From non-contact Ra surface roughness reporting to high-resolution 3D imaging and SEM analysis, our lab enables detailed inspection, prototyping support, and performance validation. This level of in-house testing is especially critical for industries like medical, aerospace, and semiconductor manufacturing—where surface finish results must be unerringly precise.
Industries That Rely on Able
Able’s expertise spans a wide range of industries with specialized standards for critical metal components:
- Medical Devices: Biocompatibility and precision finishing for implants and surgical instruments (ISO 13485:2016 and ASTM F86)
- Aerospace: Surface improvement, corrosion resistance and prep for dye penetrant testing (AS9100:2016)
- Food & Beverage: Sanitary, easy-to-clean surfaces that meet ASTM B912 and ASTM A967
- Semiconductor & Pharma: Smooth, passivated finishes that meet SEMI F19 and ASTM B912 standards
- Automotive, Hydraulics, Marine, and General Industrial: Durability and corrosion resistance across high-stress environments
Why Manufacturers Choose Able (Again & Again)
Manufacturers don’t return to Able just for the results — they return for the reliability. Every project, from prototypes to full-scale production runs, is treated with the same level of care and technical oversight. And as technologies evolve, Able invests accordingly, expanding its capabilities through automation, facility upgrades, and continuous quality improvement initiatives.
When your product’s performance, lifespan, or regulatory approval depends on metal surface quality, you need more than a vendor — you need a partner who has proven, time and again, that they’ll get it right.
That’s why companies around the world trust Able Electropolishing. And it’s why you can, too.
Interested in working with Able? Request a technical part review or send us your part to process for free to experience the difference firsthand.