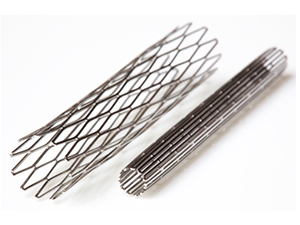
Pathogen resistance and cleanability are critical features for the makers of medical implants.
For implants made with Nitinol, an alloy prized for its elasticity, durability and “shape memory,” this requires a metal finishing process that is as specialized and powerful as Nitinol itself.
A combination of nickel and titanium, Nitinol was discovered in 1959 by the Naval Ordnance Laboratory. Lightweight and heat resistant, an early application was in missile nose cones.
Today Nitinol’s super-elasticity and ability to return to its original shape makes it a material of choice for implantable medical devices like stents, orthopedic staples, dental implants and fine-grade medical wire.
Electropolishing gives Nitinol parts the ultra-smooth, ultra-clean surface needed for medical devices, but because it is a refractory metal and extraordinarily resistant to heat and wear, it requires a chemical bath that must take place in a dedicated work cell environment. It’s a process we know well, because we helped create it.
A Process Developed to the Standards of a National Laboratory
In 2008 the Fermi National Accelerator Laboratory partnered with Able Electropolishing to develop a process for electropolishing refractory metal parts of the International Linear Collider. The result was a “mirror-like” finish to a narrow cavity within a component of the collider – and a proprietary process for electropolishing refractory metals like Nitinol that we continue to improve.
The highly-skilled team at Able Electropolishing uses those advanced processes for electropolishing Nitinol parts for a wide array of medical device manufacturers. Electropolishing removes burrs and surface imperfections from Nitinol parts with a degree of repeatable precision that other finishing processes cannot match.
For implantable medical devices made of Nitinol, like finely meshed stents, electropolishing’s ability to remove a very precise amount of material with consistent results makes it the ideal finishing process, leaving the most intricate parts more durable, cleanable and with improved fit, function and appearance.
A highly controllable process, Nitinol electropolishing can create a uniform and ultra-smooth finish within a very small diameter, leaving the smallest interior cavity free of burrs or other surface residues that other processes leave behind.
Proven, Repeatable Results for the Most Demanding Industries
At Able, our processes are carefully tested and perfected to the high standards of the industries that use our services. From medical devices and laboratories, to aerospace, pharmaceuticals and food manufacturers, we work on a wide variety of critical parts for products with no margin for error.
We are ISO 13485 certified and work closely with our clients to design the processes that will create the best results for their parts, every time, including consulting in the prototyping and design phase to help prevent issues that can impede cleanability.
Our processes are exacting, with customized chemical mixes that create the best results for each alloy or metal type, along with custom tooling and processes that include prototyping on full production equipment.
To learn more about our processes for electropolishing medical devices, including specialized processes for Nitinol parts, give us a call or click on the link below.