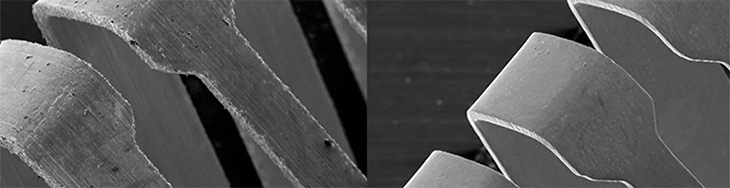
Electrical Discharge Machining (EDM) is a widely used manufacturing process known for its precision and ability to machine hard materials.
However, a common byproduct of EDM is the formation of a recast layer — a hard, brittle layer that can adversely affect the performance and longevity of machined components.
What Is an EDM Recast Layer?
An EDM recast layer is a thin, hardened layer of material that forms on the surface of a workpiece during the EDM process. This layer, which can be up to .001” thick, results from the high temperatures generated during EDM, which causes a small portion of the material to melt and resolidify rapidly. This rapid cooling leads to the formation of a layer with different properties from the base material, including:
- Increased Hardness: the recast layer is often harder and more brittle than the base material, making it susceptible to cracking and wear
- Residual Stresses: the rapid cooling process induces residual stresses in the recast layer, which can lead to distortion or failure under load
- Surface Contamination: this layer may contain contaminants from the dielectric fluid used in EDM, which can affect the surface chemistry and corrosion resistance of the component
the Problem with an EDM Recast Layer
While EDM is advantageous for creating complex geometries and working with hard materials, the recast layer poses several challenges:
1. Reduced Fatigue Life: the brittle nature and residual stresses of the recast layer can reduce the fatigue life of components, leading to premature failure in critical applications
2. Poor Surface Finish: the recast layer can have a rough and uneven surface, which may require additional finishing processes to achieve the desired surface quality
3. Compromised Corrosion Resistance: surface contamination and altered surface chemistry can reduce the corrosion resistance of the materialHow Electropolishing Solves the EDM Recast Layer Problem
Electropolishing is a process that combines an electrochemical solution with an electric current that gently removes a precise layer of material from a metal surface, providing a smooth, ultra-finished surface free of contaminants and defects.
When applied to components with an EDM recast layer, electropolishing offers several benefits:
Removal of Recast Layer
Electropolishing effectively removes the recast layer, eliminating the hardened, brittle surface and revealing the original, ductile material beneath. This enhances the mechanical properties and fatigue life of the component.
Stress Relief
By removing the recast layer, electropolishing also alleviates residual stresses induced by the EDM process, reducing the risk of distortion and cracking.
Improved Surface Finish
Electropolishing produces a bright, smooth surface that meets high aesthetic and functional standards. This is particularly important for components in industries such as aerospace, medical, and semiconductor manufacturing.
Enhanced Corrosion Resistance
The process not only removes surface contaminants but also passivates the metal, forming a protective oxide layer that enhances corrosion resistance and extends the component's service life.
Optimal Component Performance with Electropolishing
Incorporating electropolishing into the post-EDM treatment process helps manufacturers across high-risk industries such as aerospace, medical manufacturing and more ensure that their metal parts meet the highest standards of quality and reliability.
As a pioneer of the electropolishing process, Able is at the forefront of providing EDM recast layer solutions for a wide range of industries. With our expertise and advanced capabilities, we guide your project from prototyping to production ensuring that your components are free from contaminants and ready to perform at their best. Contact us today to learn more about how we can help you improve the finish, fit and function of your critical metal parts.