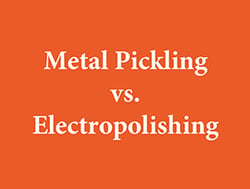
Metal pickling and electropolishing are both finishing treatments that can be used to remove surface impurities and contaminants from metal parts, but they represent two vastly different approaches in terms of process, precision and outcome. There are few applications for which pickling does not lose in a close comparison of benefits.
What is Metal Pickling?
Metal pickling is a fairly crude chemical process that uses acid, generally hydrochloric or sulfuric, to remove surface impurities like stains, rust, scale and contaminants. However, it is too corrosive for some metal alloys and has many other drawbacks, including the creation of environmentally hazardous waste.
The process is also difficult to control because the acid formulation weakens as it ages and results can sometimes be very inconsistent. It creates a chemical reaction than can liberate hydrogen that can attack the material being treated, causing hydrogen embrittlement. The result is a weakened metal part with an imprecise amount of stock removal from its surface. The process can also leave workplace windows etched from acidic fumes.
While acceptable for some industrial applications, pickling is not recommended for any parts for which the fit, function and safety depend upon a very precise and consistent level of surface material removal.
That is a key benefit of electropolishing and among the reasons it is so often specified for parts used in medical device, aerospace, dental, food processing, pharmaceutical and automotive manufacturing, among others industries.
How does Electropolishing Work?
Electropolishing, sometimes, referred to as “reverse plating,” utilizes an electrolyte bath and rectified current to remove a microscopically precise and uniform layer of surface material from parts. To begin the process, an electropolishing specialist submerses parts in a phosphoric-based electrolyte chemical bath.
A power source then converts AC current to DC at low voltages and metal ions are removed from the parts’ surfaces. Parts are then rinsed and dried. Electropolishing is a suitable treatment that provides long-lasting benefits to metal parts of a variety of common and specialty alloys, including titanium, copper, stainless steels, carbon steels, Nitinol, aluminum, tungsten and more.
At Able Electropolishing, our processes have been honed over six decades of innovation and collaboration with a wide array of industries. Our processes are customized at every step, including custom racking for each part and prototypes run on production equipment. This creates the incredibly precise and consistent results needed for critical metal parts.
Other Benefits of Electropolishing
Overall, metal pickling cannot provide the quality of metal finishing that electropolishing does. Electropolished parts benefit from a variety of improvements the process instills, including:
- Corrosion resistance—Untreated metal parts can develop rust over the course of time. Electropolishing is one of the most effective metal finishing treatments to improve corrosion resistance. Because electropolishing removes a uniform layer of surface material from metal parts, it also effectively eliminates initiation sites for corrosion.
- Microfinish value—Metal parts that have not undergone electropolishing may have micro cracks that, while not immediately concerning, could prove to be a threat to parts performance and life span. To prevent part failure, many companies submit parts for electropolishing for microfinish improvement.
- Deburring—Metal parts may have burrs or jagged edges that are unsuitable or unsafe for various applications. Electropolishing can create smooth edges by removing a thin layer from parts’ surfaces.
- Ultracleaning—Electropolishing removes the amorphous layer on metal parts, which eliminates any embedded contaminants and impurities. After treatment, metal parts can be used for applications that require sanitary or sterile objects, such as those in the food service or medical industry.
- Decorative finish—Untreated metal parts may be dull or aesthetically displeasing. Electropolishing produces a bright, shiny surface that adds an additional benefit to parts.
To learn more about obtaining the highest-quality metal finishing results for your parts, give us a call or click on the link below.