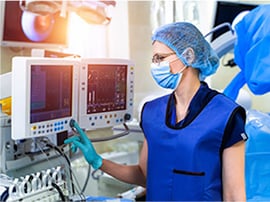
Adapting to conditions under the coronavirus (COVID-19) threat requires different things from each of us.
At Able, we remain open as an essential business throughout Illinois’ “Shelter in Place” order, helping to ensure the continued production of critical parts for clients in the medical and aerospace industries, among others.
Among the parts we have prioritized are components used in the production of medical and personal protective equipment for treating coronavirus patients, including a part used in the manufacture of N-95 masks and parts used in the production of life-saving respiratory equipment.
With three-shifts, we were recently able to put our around-the-clock production capability to use for a client working to alleviate a shortage of ventilators, expediting the electropolishing of parts used in the manufacture of this critically needed equipment.
This project called for the expedited electropolishing of over 1,000 ventilator components needed by the next morning. The parts were dropped off at 4 p.m. and our team worked through the night to complete the order for an 11 a.m. next day delivery.
As we do for each part we electropolish, we used our on-site tooling capability to create custom racking for the parts. This particular part required the additional step of masking to ensure that only a certain area of each part was exposed for electropolishing. Robotic automation helped ensure the speed and consistency of the process.
Electropolishing for Safer, Pathogen-Resistant Medical Device Parts
Electropolishing for medical device parts creates an ultra-smooth surface free of imperfections that can trap liquids and debris and impede cleanability. Electropolishing also creates a corrosion and pathogen-resistant surface with a microscopically precise and consistent amount of material removal that improves the fit, finish and function of critical medical parts.
Our processes, honed over six decades of innovation and collaboration with our clients in the medical manufacturing industry, help ensure the safe, reliable and rapid production of a wide variety of medical devices and instruments and we are proud to be able to continue our efforts throughout these difficult circumstances.
To learn more about electropolishing for medical device parts and instruments, give us a call or click on the link below.
We are also available to consult in the design and prototyping process, as part of our Finish First methodology, through which we can help prevent design flaws that can impact the ability to achieve the highest-quality metal finish.
Learn More about Electropolishing for Medical Device Manufacturing